About Course
A Cell Equipment Maintenance Supervisor is responsible for overseeing a team of technicians and ensuring the reliability of cell manufacturing equipment. They manage maintenance schedules, conduct performance evaluations, and provide technical guidance. Supervisors ensure that equipment is well-maintained to maximize production efficiency. They also enforce safety protocols and maintain a safe working environment. Their role contributes to consistent and smooth production processes in the cell manufacturing facility.
What Will You Learn?
- The learning outcomes for a Cell Equipment Maintenance Supervisor typically encompass a combination of technical skills, leadership abilities, and management competencies necessary to oversee and coordinate the maintenance of equipment within a cellular manufacturing or production environment. Here are some key learning outcomes for a Cell Equipment Maintenance Supervisor:
- 1. Technical Proficiency
- 2. Safety and Compliance
- 3. Equipment Documentation
- 4. Team Leadership
- 5. Problem-Solving Skills
- 6. Resource Management
- 7. Budgeting and Cost Control
- 8. Continuous Improvement
- 9. Communication Skills
- 10. Emergency Response
- 11. Inventory Management
- 12. Training and Development
- 13. Data Analysis
- 14. Documentation and Reporting
- 15. Customer Focus
- These learning outcomes are crucial for someone aspiring to become a Cell Equipment Maintenance Supervisor, as they need to balance technical expertise, leadership, and management skills to ensure the smooth operation of equipment in a manufacturing or production setting.
Audience
- Qualification: BE/ Betch
- Age: 24+ Years
- Experience: 3+ Years
Course Content
Basics to PV Cell
Photovoltaic (PV) cells, often referred to as solar cells, are the fundamental building blocks of solar panels. These cells are semiconductor devices that convert sunlight into electricity through the photovoltaic effect. When exposed to sunlight, PV cells generate a flow of electrons, creating a direct current (DC) electrical output. Multiple PV cells are interconnected within solar panels to produce usable electricity. PV cells are crucial in harnessing renewable solar energy and contribute to sustainable power generation, making them a key component of the global transition toward clean and green energy sources. Understanding the basics of PV cells is essential for anyone involved in solar energy production and related industries.
-
Basics of Semiconductor
00:00 -
Solar Cell Principles & Production Environment
00:00 -
Short Review-1
Cell Quality
Cell quality in cell manufacturing process refers to the standard of photovoltaic (PV) cells produced, which directly impacts the efficiency and performance of solar panels. It encompasses aspects like cell uniformity, material purity, electrical characteristics, and defect detection. Maintaining high cell quality is essential for optimizing the energy output and durability of solar panels, ensuring their long-term effectiveness in harnessing solar energy.
-
KY-SOP-CL-002 Standard operating procedure for LID and LeTID
00:00 -
KY-SOP-CL-003 Standard operating procedure for cell shop cleanliness testing
00:00 -
Establishment of Sorting Rules
00:00 -
7 Big Techniques of QC
00:00 -
KY-QIS-CL-002 Incoming inspection standard for wafer
00:00 -
KY-QIS-CL-003 Incoming inspection standard for cell packaging materials
00:00 -
KY-QIS-CL-004 Incoming Inspection Standard for Cell Paste
00:00 -
KY-QMR-CL-006 Cell Quality Control Plan
00:00 -
Finished Product Appearance Inspection Standard Training
00:00 -
Finished Product EI Inspection Standard Training
00:00 -
KY-SOP-CL-001 Standard Operating Procedure for Cell Electrode Tension Test
00:00 -
KY-SOP-CL-004 Standard Operating Procedure Cell Electrode Welding Operation
00:00 -
KY-QMR-CL-001 Standard Sampling Specification for Finished Cell Products
00:00 -
KY-QIS-CL-005 Incoming Inspection Standard for Cell Screen
00:00 -
Classification Detection & EL Process
00:00 -
Solar Cell Cost Reduction & Efficiency Improvement Training
00:00 -
Cell Reliability Test-1
00:00 -
Cell Reliability Test-2
00:00 -
Quick Review
Equipment Maintenance
Equipment maintenance involves planned activities to ensure machines, tools, and systems remain in optimal working condition. It includes routine inspections, repairs, and preventative measures. Proper equipment maintenance extends the lifespan of assets, reduces downtime, enhances safety, and boosts operational efficiency. It is a crucial aspect of facility management and manufacturing, helping to minimize unexpected breakdowns and costly repairs. Regular maintenance routines follow schedules, manuals, and manufacturer recommendations to ensure reliability and safety.
-
Solar Cell Cost Reduction & Efficiency Improvement Training
00:00 -
RENA Texturing Equipment Training
00:00 -
RENA Etching Equipment Training
00:00 -
Training on Low-Pressure Diffusion Equipment
00:00 -
Training on High Temperature Oxidation & Annealing Furnace Equipment
00:00 -
Training on PECVD Equipment
00:00 -
MAIA Equipment Training
00:00 -
Operating Manual of Sintering Furnace
00:00 -
ANTI-LID Equipment Debugging
00:00 -
SMDF-6.1__en__MaintPlan
00:00 -
SMDF-6.1__en__Operation Manual
00:00 -
Technical Description_MAiA6.1_SiNOx
00:00 -
BatchTex_Part1-UsersGuide
00:00 -
InOxSide_Part1-UsersGuide
00:00 -
Quick Review-2
6s Occupational Health, Safety, and Environment (OHSE)
6S Occupational Health, Safety, and Environment (OHSE) refers to a systematic approach to workplace management that focuses on safety, cleanliness, and efficiency. It involves maintaining a safe and organized work environment, ensuring proper waste disposal, and fostering a culture of responsibility and sustainability. This framework aims to enhance employee well-being, minimize hazards, reduce waste, and promote environmental awareness within the workplace. 6S OHSE principles help organizations improve overall safety and environmental performance while increasing productivity and employee engagement.
-
Workshop Management System Training
00:00 -
Common Sense of Workshop Environmental Safety
00:00 -
Team Safety Handout
09:07
Manufacturing Execution System
A Manufacturing Execution System (MES) is a software-based solution that facilitates real-time monitoring, control, and management of manufacturing operations. MES systems help optimize production processes, improve quality, and enhance overall productivity by collecting and analyzing data from various sources on the shop floor. They enable better decision-making and communication among different departments within a manufacturing facility. MES can track and report on key performance indicators, providing valuable insights to enhance operational efficiency and streamline production activities. MES plays a crucial role in modern manufacturing, supporting Industry 4.0 initiatives and the digitization of factories.
-
MES System Theory & Application in Production
00:00 -
MES System Architecture
00:00 -
Data Acquisition System Introduction
00:00 -
Network & Hardware Equipment Theory
00:00 -
Quick Review-3
Workplace help and Resource
Workplace Help and Resources refer to the support and materials available to employees to enhance their productivity and well-being. This includes access to assistance for technical issues, HR inquiries, and training materials. Providing these resources fosters a positive work environment and empowers employees to perform at their best. It can also include health and wellness programs and information to support employees' physical and mental health. These resources are vital for addressing employee needs and improving overall workplace satisfaction and effectiveness.
-
New Employee Orientation, Personnel System Training
00:00 -
Induction Training for New Employees
00:00 -
Ability to Execute
00:00
Tags
Instructors
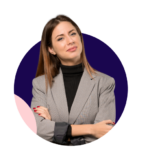
RENX Academy
RENX offers best-in-class training solutions to various Industries and Manufacturing facilities. The courses have been tailormade for Various Skilled Technicians, Operators, Executives, Integrated line workforces, engineers and all kinds of associated partners for helping organisations to meet their manufacturing excellence.
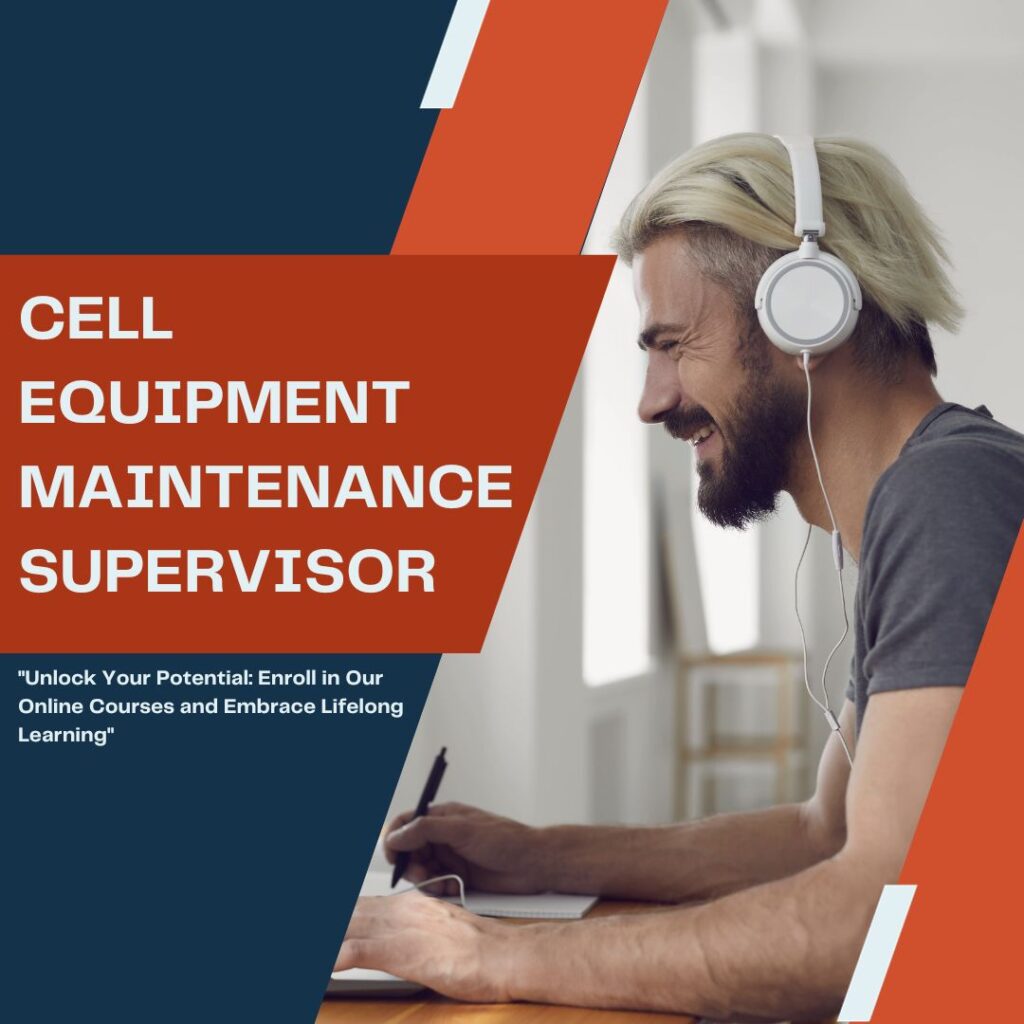
- Intermediate
- 300 hours
- April 16, 2024
- Certificate of completion